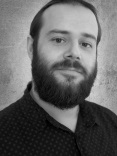
Michael Schneider
Institute of Sensor and Actuator Systems, Austria
Biography
Michael Schneider studied physics at the Karlsruhe Institute of Technology from 2003-2009. He performed his diploma work at the Forschungszentrum Karlsruhe on the measurement of Lorentz angles in highly irradiated silicon strip detectors for high energy collider applications, such as the large hadron collider at CERN. He finished his studies in 2009 and started his PhD thesis on the optimization of ultra-thin aluminum nitride films for actuation and sensing applications in micro electromechanical systems at the Department of Microsystems Technology at TU Vienna. He received his PhD in 2014 and is currently working as a postdoc on advanced materials such as silicon carbide and doped aluminum nitride, as well as MEMS devices based on piezoelectric thin films.
Abstract
Electromechanical transducers based on the piezoelectric effect are continuously finding their way into micro-electromechanical systems (MEMS), typically in the form of thin films. Piezoelectric transducers feature a linear voltage response, no snap in behavior and can provide both attractive and repulsive forces. This removes inherent physical limitations present in the commonly used electrostatic transducer approach while maintaining beneficial properties such as low power operation. Furthermore, piezoelectric materials can serve for both actuation and sensing purposes, thus enabling pure electrical excitation and read out of the transducer element in combination with a compact design. Based on these outstanding features, piezoelectric transducers are operated most beneficially in a large variety of different application scenarios, ranging from resonators in liquid environment, advanced acoustic devices to sensors in harsh environments. In order to exploit the full potential of piezoelectric MEMS in the future, interdisciplinary research efforts are needed ranging from investigations of advanced piezoelectric materials over the design of novel piezoelectric MEMS sensor and actuator devices to the integration of Piezo MEMS devices into full low-power systems. In this presentation, we will highlight latest results on the electrical, mechanical and piezo electrical characterization of sputter-deposited aluminium nitride (AlN) including the impact of sputter parameters, film thickness and substrate pre-conditioning. We will present the impact of doping of AlN with scandium, which leads to an increase of the moderate piezoelectric coefficient of AlN upto a factor of four. We will also present first results on the piezoelectric co-polymer PVDF TrFE. In next step, these films are implemented into fabrication processes of cantilever type MEMS devices. In combination with a tailored electrode design resonators are realized featuring in liquid Q-factors upto about 300 in the frequency range of 12 MHz. This enables the precise determination of the viscosity and density of fluids upto dynamic viscosity values of almost 300 mPas. Besides this application, such as high Q factors are useful when targeting mass sensitive sensors, thus paving the way, for e.g., particle detection even in highly viscous media. Given the low increase in permittivity of ScAlN compared to AlN, another field of application for this functional material class is vibrational energy harvesters, where the benefit of ScAlN compared to pure AlN is demonstrated. Finally, we will present some selected results of ScAlN thin films within SAW devices ranging from high temperature applications to droplet manipulation in microfluidics.